WNS Series Boiler
Gas/Oil Fired Steam/Hot Water Fire Tube Boilers. The WNS series is a complete range fire tube boilers from 1MW through to 13MW. The WNS series boiler is available for either a steam or hot water applications and are fired on either gas or oil.
Easy to use and approved for unattended operation. Our boiler control systems are designed and built in-house using the latest technology. Some of the features offered are trending and optional SMS messaging.
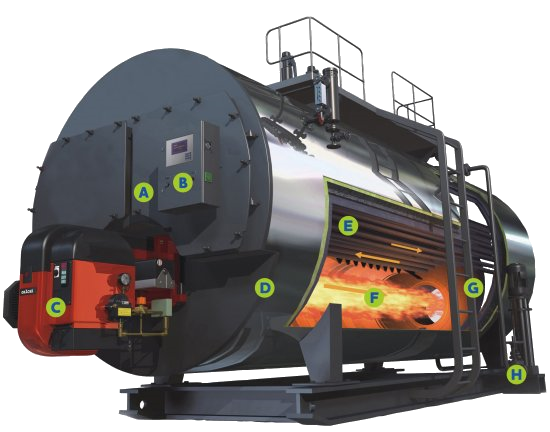
These boilers are supplied as a complete turn-key package including burner, feed water pumps and control system. The WNS series is a modern three pass boiler design right from the smallest through to the largest in the range. The WNS series boilers are built to the highest quality standards and provide the highest efficiency available of any boiler design. The WNS series boiler is fitted with a high quality European burner using the latest digital air/fuel ratio control system. Gas, oil and dual fuel options are available as standard. Flue gas oxygen trim and burner fan VSD options are available through the entire range. These burner offer the highest efficiency and reliability available anywhere in the world.
The boiler is supplied complete with an approved unattended control system built around a user friendly touch screen interface. Clean graphics and simple intuitive layout ensure the control system is easy to navigate and operate.
Flue gas economisers and flue gas condensers are available across the entire WNS boiler range. These maximise efficiency. We have customers running with flue gas temperatures on 13,000kW boilers as low as 40 Degrees Celsius. These improvements could lower your operating costs by as much as 10%.
Our WNS series boilers are an innovative modern design and not based on outdated 1960’s technology. These boilers incorporate a large, fully corrugated furnace, providing excellent expansion flexibility, increased surface area and strength. A large water cooled reversal chamber is incorporated in the three pass wet back design and ensures maximum efficiency. The WNS boiler design incorporates features that reduce the effects of thermal cycling and manufacturing processes to ensure these high quality products stand the test of time. These features apply across the entire range of this product, regardless of size.
The WNS range of boilers are designed and manufactured to BS EN 12953, this is a well recognised boiler manufacturing standard here in new Zealand. The WNS boilers are also manufactured under an ISO9001 quality management system. In addition, third party inspections, by a Worksafe approved inspection body are also carried out to independently verify quality during and after the manufacturing process.
Our WNS series Steam and Hot Water boilers provide a gross efficiency from 84% for the lowest specification up to an unprecedented 90% gross for boilers fitted with condenser options. A large combustion space with increased surface area provides superior energy transfer from the combustion gas into the water reducing stresses on the rear tube plate. The fire tubes have a scroll rolled into the outer of the tube, enabling steam bubble formation to migrate around the tube to the surface of the water and into the steam space. These scrolled fire tubes also promote combustion gas turbulence within the tube, improving heat transfer and further increasing efficiency.
The superior triple layer insulation system on the WNS series boilers comprises a high density insulation layer attached to the shell of the boiler and covered by a thick silver reflective blanket to reflect lost heat back inward, encompassed by a thick layer of fibre glass insulation and then clad in an outer layer of stainless steel. In addition, both the second and third pass combustion gas reversal chambers are internally lined with refractory and insulation, a unique feature to this boiler range. This insulation provides extensive heat retention in the combustion gases and reduces radiant and conductive losses to atmosphere, achieving optimal flue gas efficiency and exterior boiler surface temperatures typically below 50°C.
Each model of WNS boiler range incorporates a large steam space and steam scrubber, providing high quality steam even under varying loads. This high quality steam eliminates unnecessary condensate in the steam, ensuring superior heat exchange in the process equipment, reducing overall fuel consumption and scaling.
Optimal boiler efficiency provides superior boiler performance, reducing the amount of fuel required to achieve the same boiler output. Flue gas exhaust temperatures for boilers fitted with condenser options are as low as 40°C. That’s as much as 250°C lower than conventional two pass dry back designs. This reduces fuel consumptions and therefore reduces the impact on the environment and the overall ongoing operational costs associated with the boiler. Flue gas economisers and condenser options are available to suit any WNS boiler in the range.
Our use of high quality European equipment on our package boilers includes Spirax Sarco, Gestra & Ari valving and control equipment, Oilon burners, complete with Siemens LMV5x control system and multi-stage Grundfos feed-water pumps. The quality of this equipment ensures superior control, maximum efficiency and ongoing reliability.
Our market leading package boiler control system is modelled around a PLC with large colour touch screen interface. A Siemens LMV5x digital combustion manager provides accurate and repeatable burner control and maximum efficiency. Spirax Sarco equipment is utilised for low water level protection, Gestra instrumentation and valving is used for automated blow down control. Our Oilon burner range provides maximum combustion efficiency, operating at low excess air levels. In addition, we can offer variable speed combustion fan control and automated oxygen trim to further optimise electricity and fuel savings for the life of the boiler. The control system provides detailed boiler fault descriptions, trending and testing functions. Cellular modems can be provided to allow the ability to contact responsible persons assigned to the boiler via cell phone or pager, with a description of the actual fault when required. PLC addresses can also be supplied to allow your site BMS to display boiler information and faults.